A hair dryer factory is a complex operation involving a variety of processes and machinery. From the initial cutting and molding of metal to the final packaging and shipping, hair dryers undergo a series of complex processes and steps. Each stage of the production process contributes to the efficient and effective performance of a hair dryer.
Each hairdryer has its own unique design, but they all have two basic components. First, the hairdryer body consists of a plastic shell that has two sections. This shell is made using a process called injection molding. Injection molding involves injecting hot plastic into a stainless steel die. Cooling the plastic around the die makes it harden and the parts can then be removed. Each side of the plastic shell has several holes, while the other half features short pins that aid in alignment of the two halves.
Next, the dryer's nozzle is a crucial component. When designing the nozzle, manufacturers must consider how heat is distributed and what kind of use will the dryer be used for. As a result, each hair dryer has a unique nozzle design. It is this design that plays a big part in how well it works.
As hair dryers are so hazardous, special safety measures must be taken to protect consumers. To protect consumers, manufacturers must include a warning picture on the appliance. The warning picture should be permanently attached to the drier's cord. Additionally, polarized plugs help ground the appliance, preventing accidental shocks. In addition, manufacturers must follow requirements to avoid short circuits when the device is turned on.
Hair dryer production is an intricate process that involves complex machinery and processes. The products go through several stages during the production process, from design to packaging, and from shipping to marketing. This makes it difficult to keep track of the entire process. Fortunately, there are ways to stay abreast of the progress of the production process in order to ensure quality control.
Hair dryers have two main parts: the plastic shell and the heating element. The plastic shell is made by injection molding, where hot plastic is injected into a stainless steel die. Then, a circulating stream of cold water cools the plastic, making it harden and durable. Once the die is opened, the plastic parts are extracted from the mold. The plastic shell has holes on one side, and the other half has a series of short pins to help align the two parts during manufacture.
In the United States, the Consumer Product Safety Commission (CPSC) established safety guidelines for hair dryers in the 1970s. By 1991, they were required to have a ground fault circuit interrupter (GFCI) to prevent accidental electrocution. These changes helped reduce the number of blowdryer deaths from hundreds to four per year.
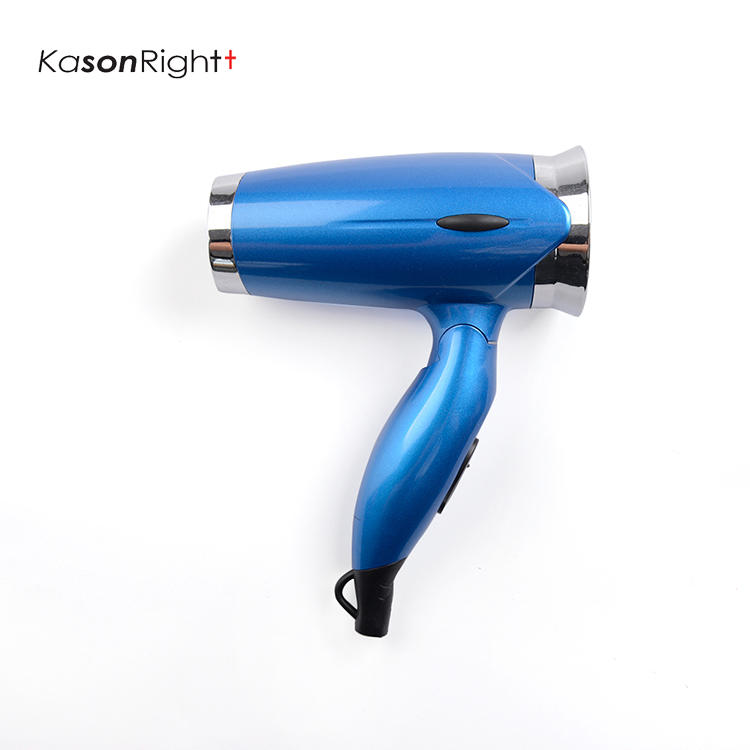
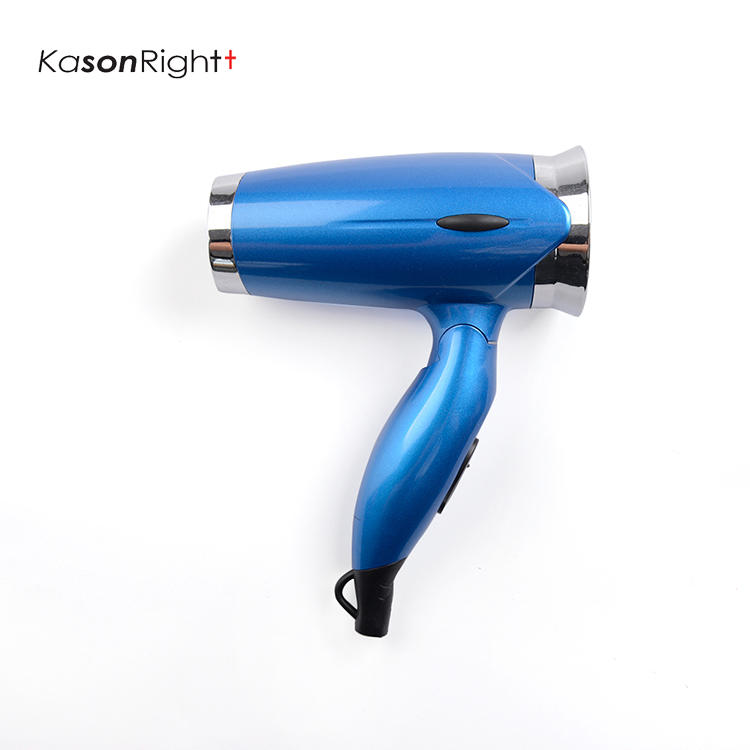